It was wonderful watching my workshop being constructed on Wednesday. It was like having an actual life HGTV present occurring proper in my again yard, and it virtually appeared to occur as quick as these unrealistic exhibits. The entire workshop, from starting to finish (not together with the storage door set up) was constructed, painted, and shingled in a span of lower than 27 hours. The entire construction was constructed and painted on the primary day, after which yesterday, they returned to put in the entrance door, shingle the roof, and strap down the anchors. The corporate I used contracts out the set up of storage doorways, in order that they got here later within the after yesterday.
Right here’s the way it appears to be like now that it’s utterly completed.


And naturally, after I say it’s completed, what I imply is that their half is completed. Now it’s as much as me to take this from plain to cute, and I’ll do this by including blue shutters, a coral entrance door, window flower containers, entrance steps, skirting, and a fringe of gravel round the entire thing. And naturally, I’ll add some potted crops by the door. However for now, I’m simply pleased to have the constructing, at the same time as plain as it’s.
I took footage of the entire course of, and despite the fact that this wasn’t a DIY undertaking for me, it may very simply be a DIY undertaking for a few of you. The method itself is just not tough. The place the issue is available in is that this isn’t a one-person undertaking. You’ll positively want some assist, and that assist must be (1) helpers who’ve muscle (for at the least some elements of the method), and (2) helpers who aren’t afraid of heights (for the roof). But when you’ll find helpers like that, this might very simply be a DIY undertaking, though I doubt that will probably be a 27-hour undertaking.
There are just a few causes these guys had been capable of construct this so quick:
- They do that day-after-day and have the method down so nicely they may in all probability construct these of their sleep. Watching them do that was like watching a choreographed dance. Every particular person knew their half and didn’t miss a beat.
- After they arrived, about 99% of each piece of lumber, plywood, and all the things else they wanted was already reduce to the precise dimension they wanted. That is completed of their store based on the measurements of the constructing. Not having to chop plywood and lumber to dimension on website saved a ton of time.
- These buildings aren’t constructed like homes. On a home, partitions are usually raised once they’re simply on the framing stage (solely 2″ x 4″ lumber). As soon as the framed partitions are raised, then they’re coated with OSB, home wrap, after which siding, in three separate steps. However with these buildings (my workshop is only a massive, glorified shed), they use a product that mainly has the home wrap, OSB, and siding multi function product. So it will get utilized in a single step as an alternative of three.
However even with these benefits and time-saving steps, it was nonetheless wonderful to see this go from nothing to completed in such a brief period of time. And let me let you know one thing, these guys are laborious staff!! They labored nonstop from 7:30am to 4:30pm, with solely a few 30- or 45-minute lunch break. (I wasn’t right here once they went to lunch, so I’m unsure precisely how lengthy they had been gone. But it surely couldn’t have been longer than 45 minutes.)
Anyway, let me get on with the method.
Laying out and connecting the skids
My constructing is eighteen′ x 27′, and for this dimension constructing, they used 4 of those massive beams known as skids. I didn’t measure them as a result of I didn’t wish to get of their approach, however these appeared to be 4″ x 6″. These went the size of the constructing (27′).


As a result of these skids don’t are available that size, they needed to piece two collectively for every 27′ run. You may see the place they’ve two laid out end-to-end for every one.
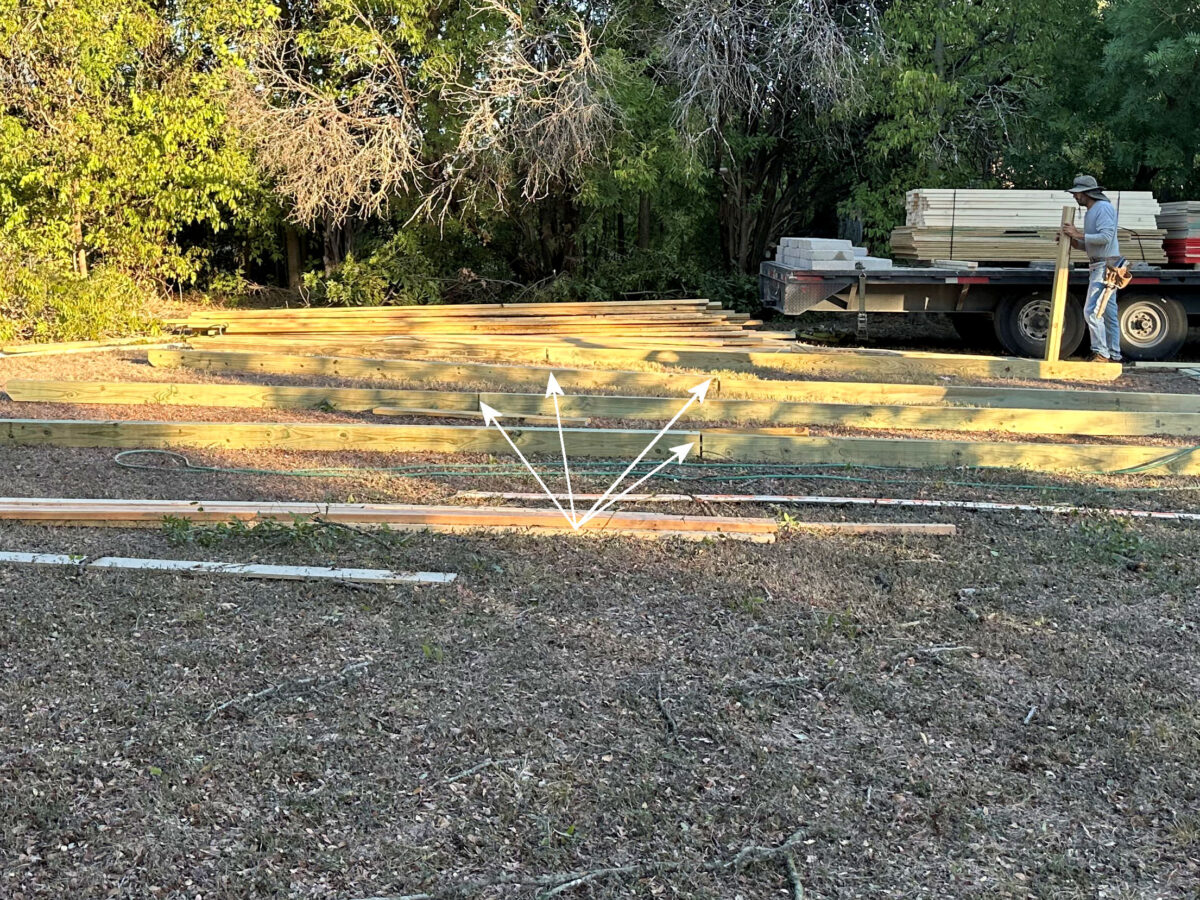
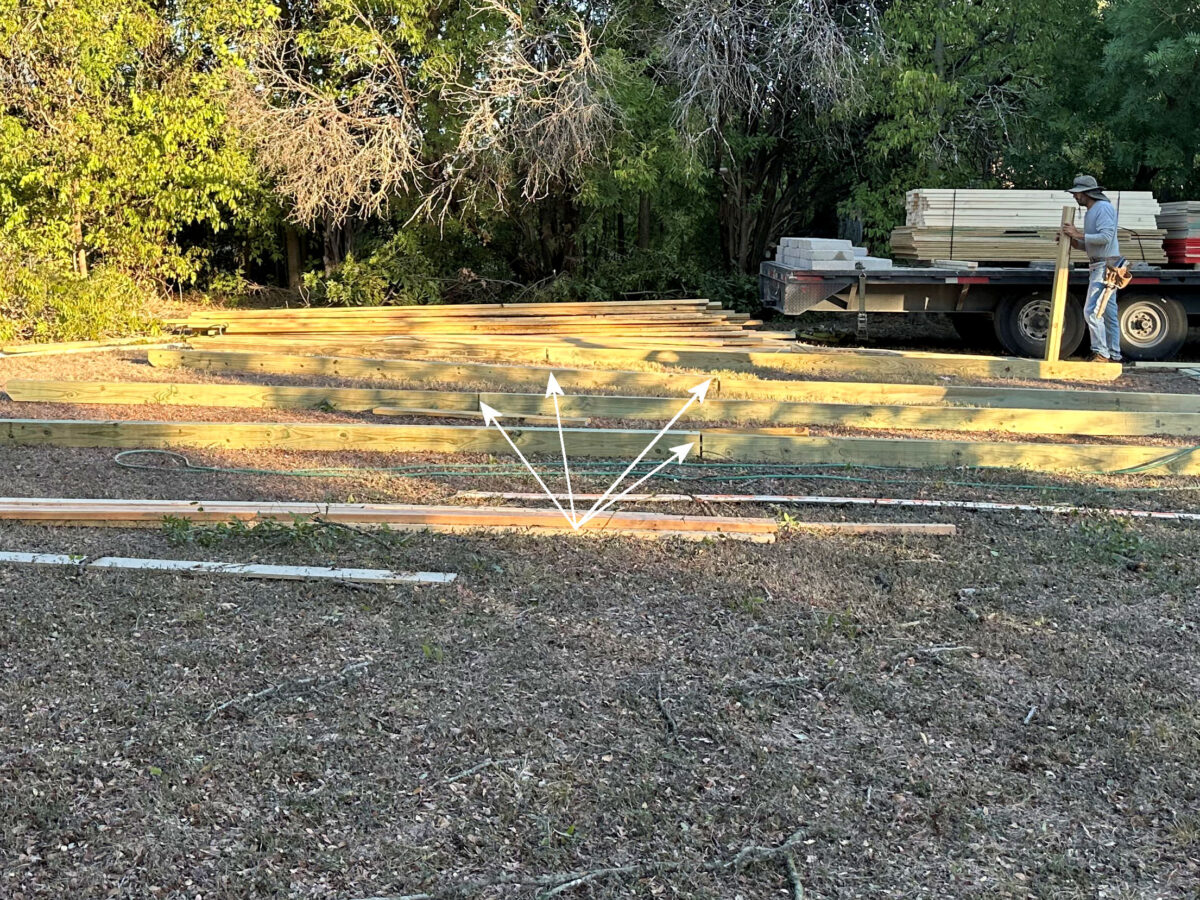
To safe these collectively, they used lengthy items of 1″ lumber nailed to every aspect of the skid over the realm the place they linked. I didn’t get an image of that once they did it, however you’ll be able to see it right here…


Constructing the muse
As soon as they’d all 4 skids assembled, they hooked up these boards, which had been both 2″ x 8″ or 2″ x 10″ boards, and nailed them on in order that the boards had been mendacity flat. These boards overlapped the perimeters of the skids by about 10-12 inches, and overlapped the ends of the skids by just a few inches as nicely. It was nailed to the skids in order that the skids had been 4′ aside.


You may see that board right here. They used about 20 nails via that board into every skid. I received somewhat behind in my image taking and didn’t get a detailed up image till the muse was completed, however the board with the arrow is the one which was hooked up first.
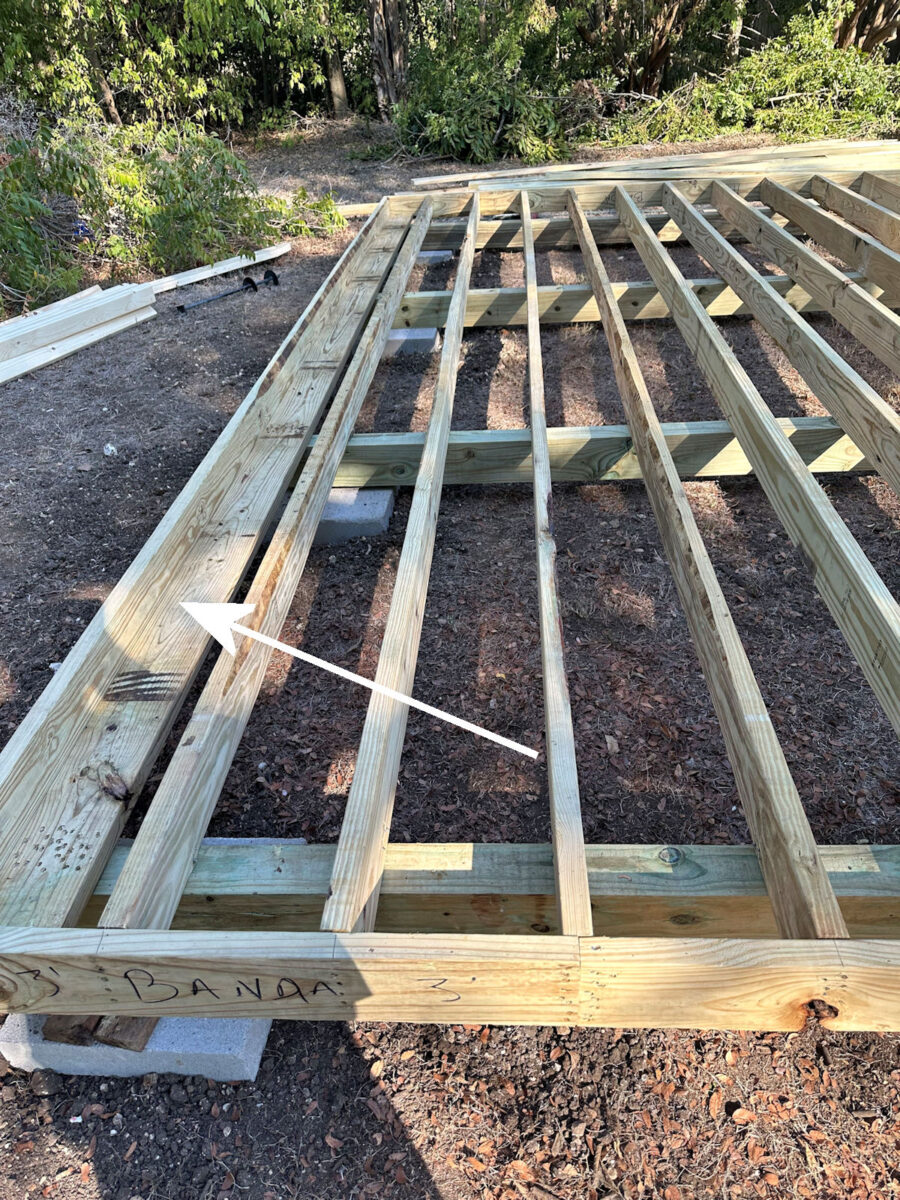
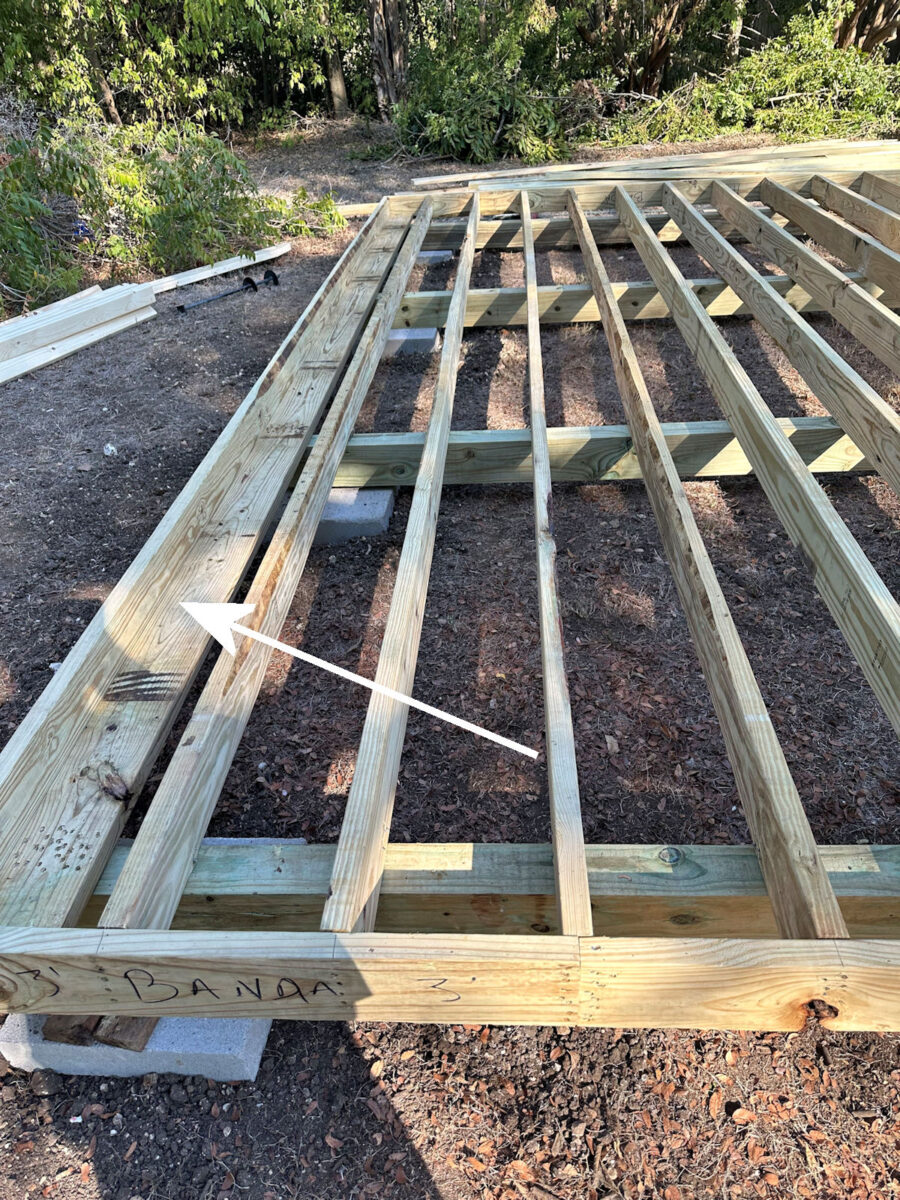
After these two boards had been hooked up (one on every finish), they used that to construct a fringe body utilizing 2″ x 6″ lumber standing up on finish. This perimeter body was nailed into these two earlier boards.
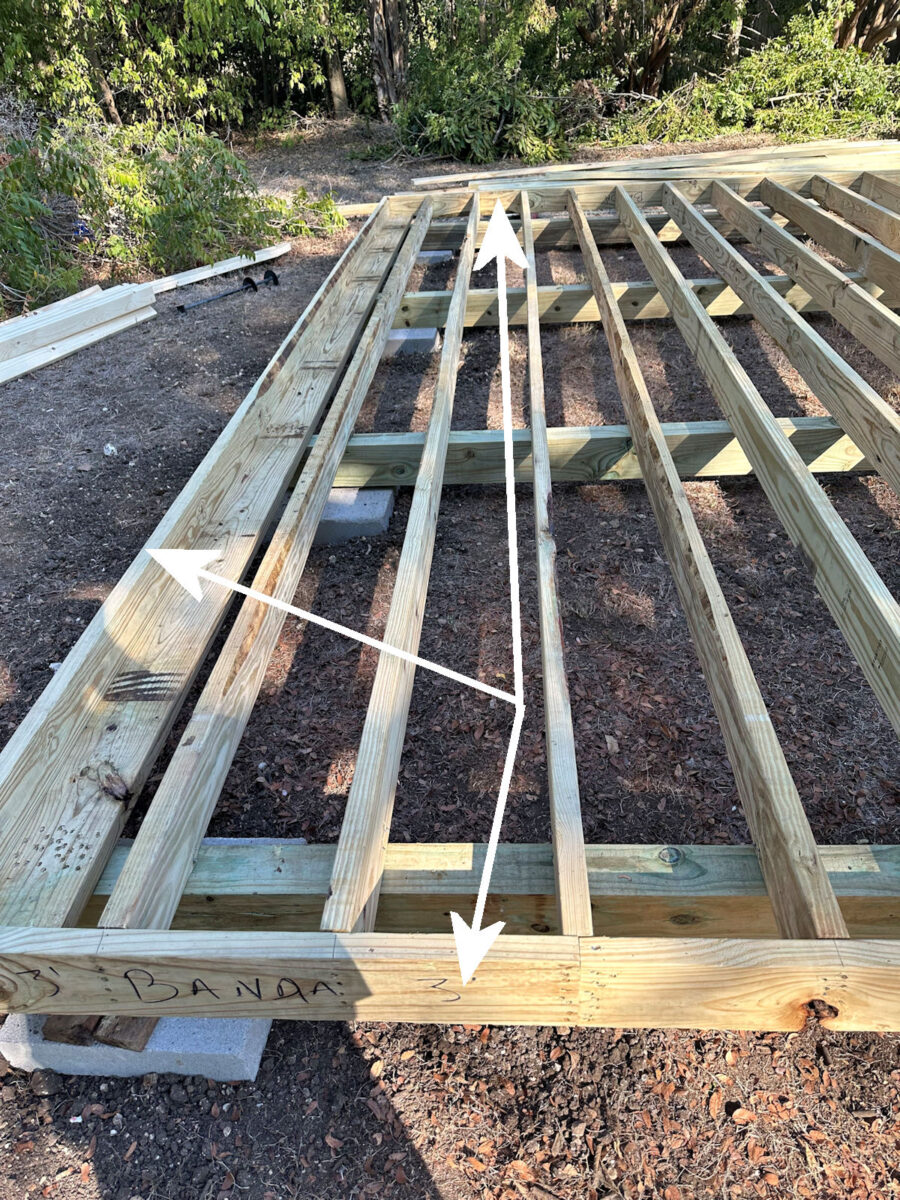
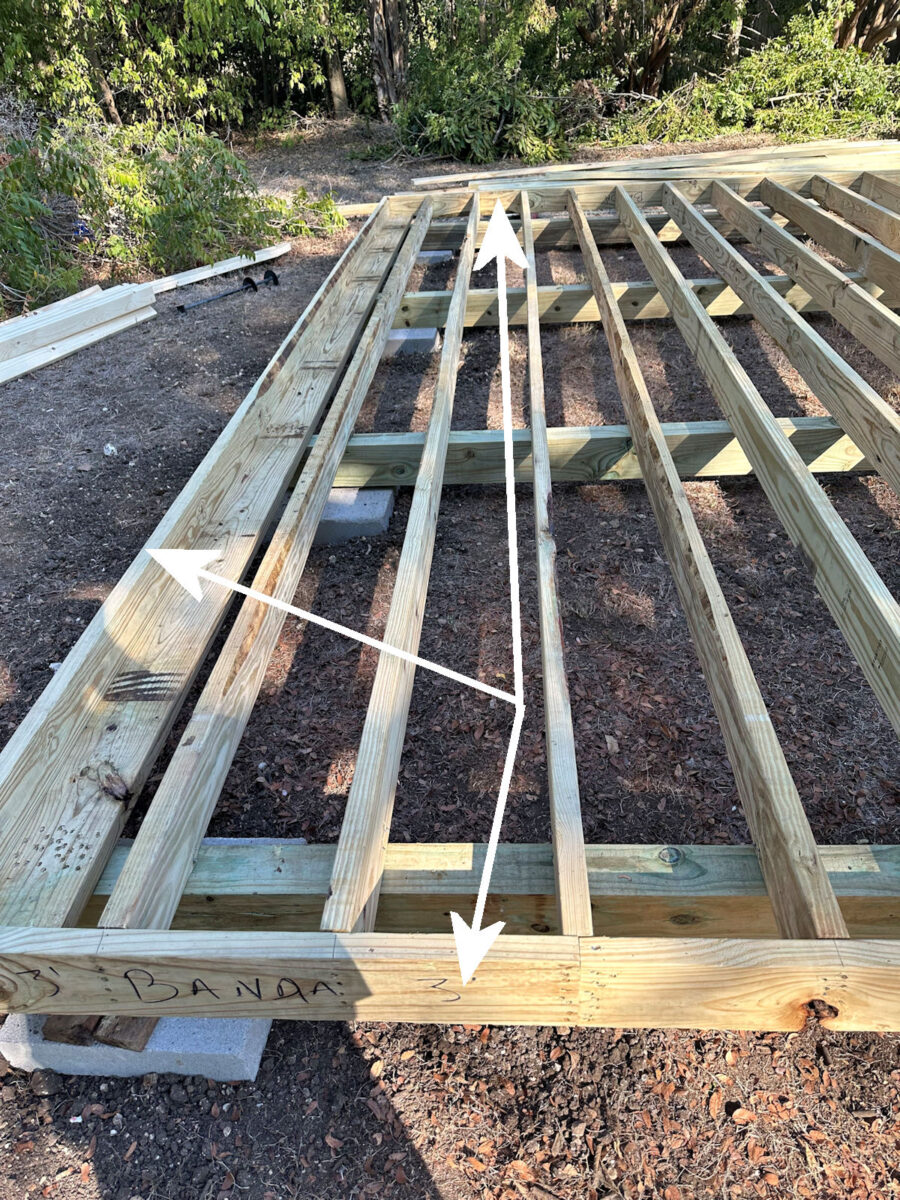
After that perimeter body was nailed into place, they went again and added the ground joists (additionally 2″ x 6″ lumber) positioned 16 inches aside on heart.
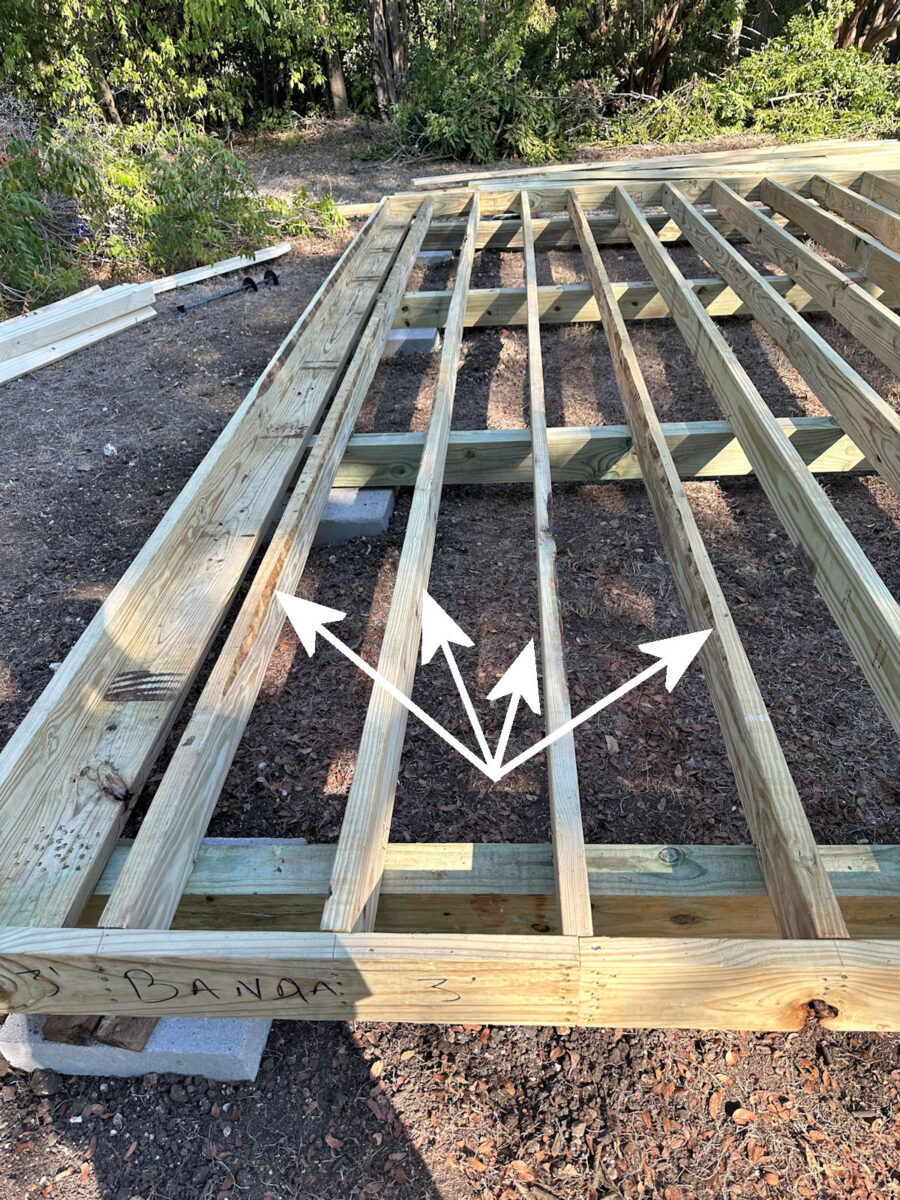
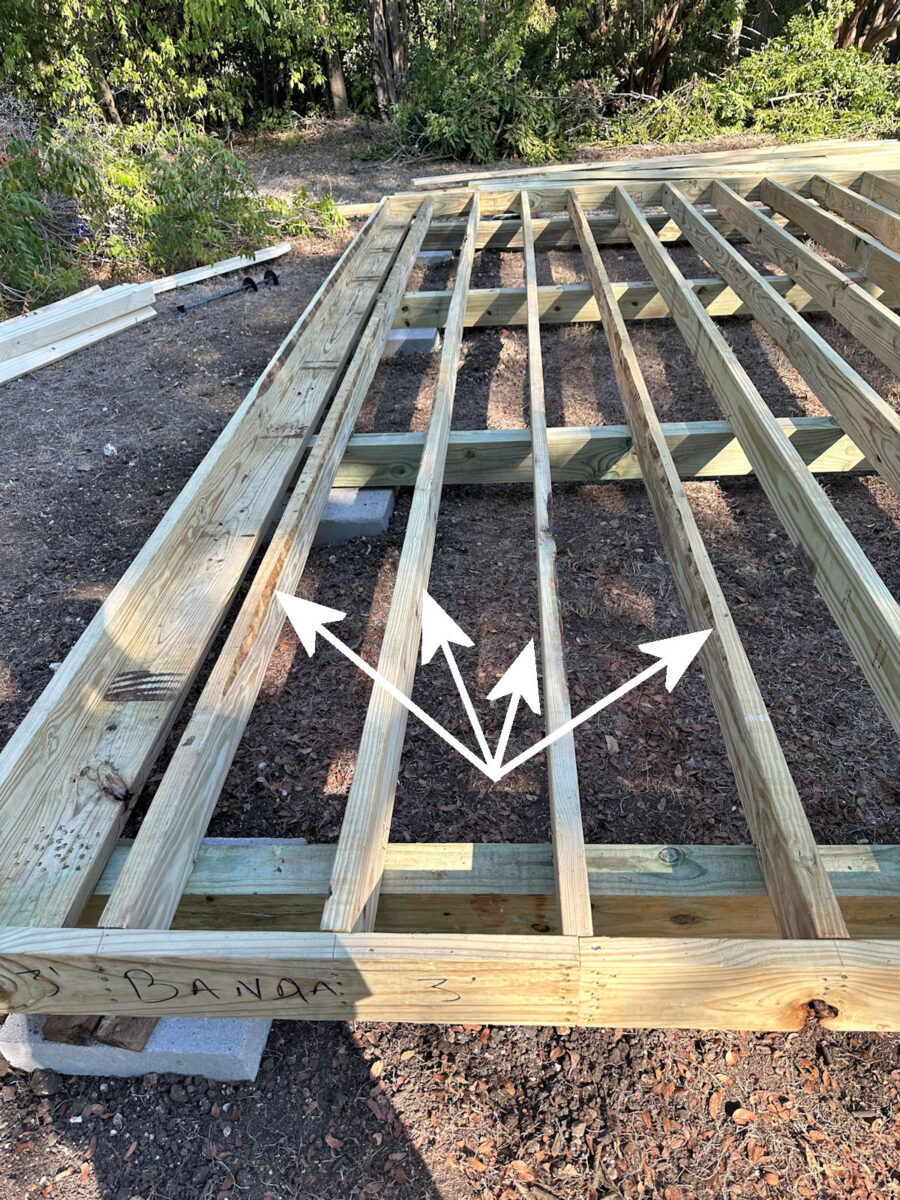
Like I mentioned, I received a bit behind on my image taking (I didn’t wish to get of their approach), however they really constructed your entire basis immediately on the bottom (i.e, the skids had been immediately on the filth), after which they went again and added the concrete blocks. After the concrete blocks had been added, they then leveled the muse utilizing a jack and shims. I didn’t get an image of that, but it surely ought to be fairly self-explanatory.
At this level, they used this machine, which was like a really sluggish turning auger, to put anchors into the bottom. For a constructing this dimension, town required six anchors, three on every lengthy aspect.
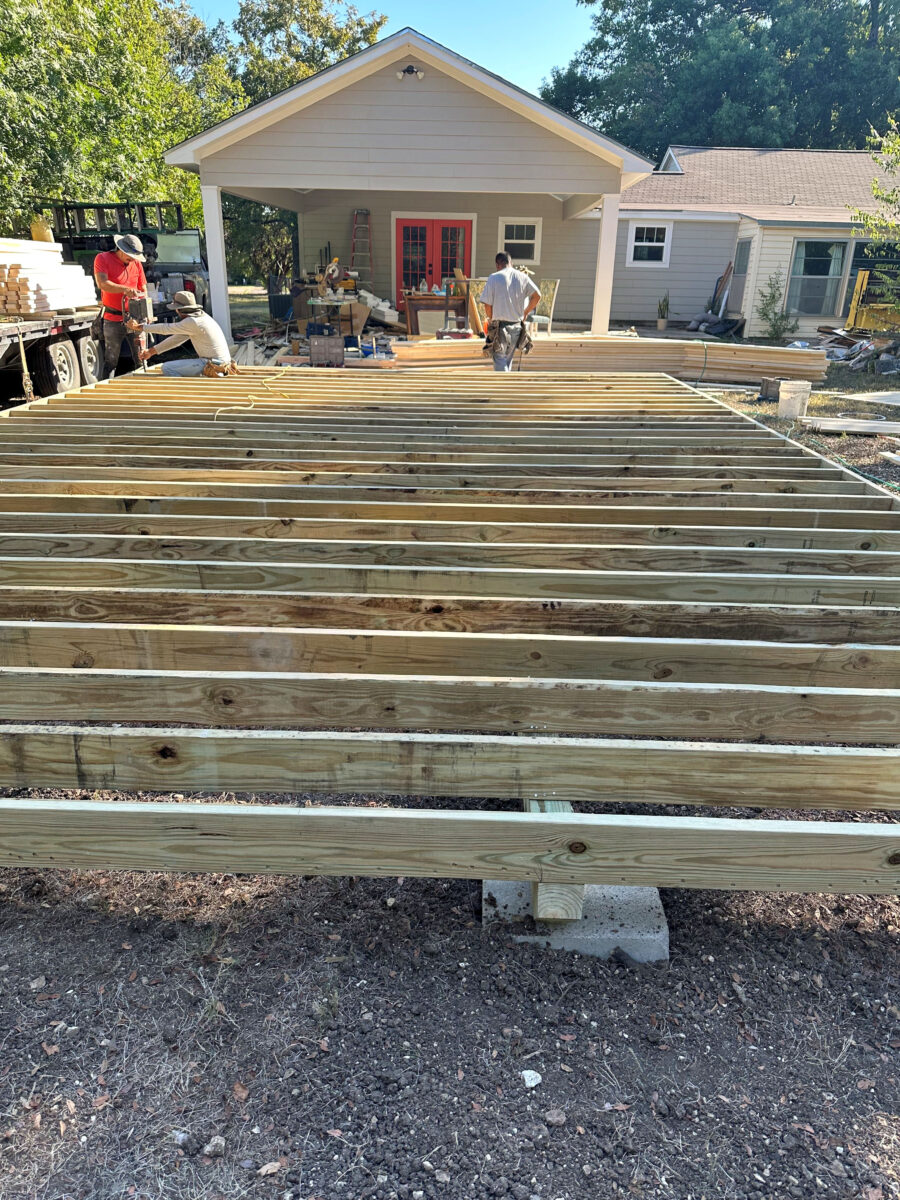
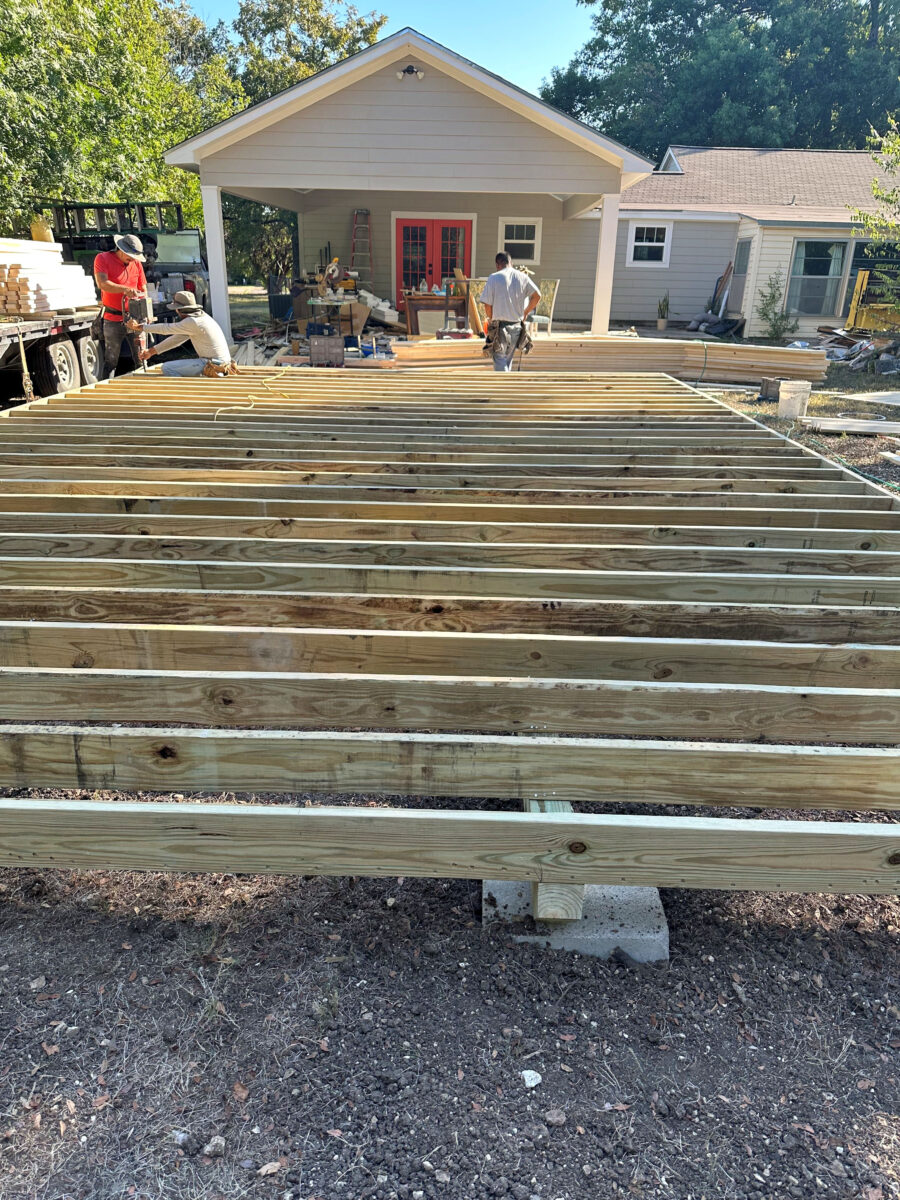
These are the identical anchors which are used for tying down cellular properties. They’re 30 inches lengthy and have spikes that maintain them within the floor. They didn’t truly strap it down at this level as a result of they wanted to have the ability to make changes because the constructing was being constructed. However they needed to get the anchors in place whereas these areas had been nonetheless accessible.


You may see one of many anchors protruding of the bottom right here…


And with that, the muse was completed. Right here’s one other take a look at one finish so you’ll be able to see all the elements of the completed basis.


And right here’s a distinct angle…


Including the subfloor
Subsequent, they added these strips of plastic (it appears to be like like Tyvek-type home wrap) each 4 toes the place the subfloor plywood would meet. (Once more, I reiterate that these buildings aren’t constructed like a home. However if you happen to’re doing it your self, I’d think about you possibly can wrap your entire factor if you happen to needed to.)


After which they hooked up the subfloor, which is 3/4-inch plywood, and nailed that to the ground joists and perimeter body.


Constructing the partitions
As soon as the subfloor was put in, they moved on to constructing the partitions. They began with the entrance wall (i.e., the wall with the entrance door and two home windows).


Right here’s a take a look at how a wall is constructed. It begins with a horizontal 2″ x 4″ board on the backside. That is known as the bottom plate or sole plate. Perpendicular to the bottom place are the studs. These are spaced 16 inches on heart. After which on the high is one other horizontal 2″ x 4″ board. That is known as the highest plate. I’ve solely ever seen the highest plate include two stacked 2″ x 4″ boards, however they did one 2″ x 4″ and one 2″ x 8″ board. All of it is smart later.


Within the above image, you may also see how a window opening is framed. It begins with a load-bearing header on the high. That header is manufactured from two 2″ x 6″ items with a bit of plywood sandwiched in between to make it 3.5 inches thick. After which a 2″ x 4″ piece of lumber is nailed to the highest, and one other one is nailed to the underside. That total meeting makes up one load-bearing header for a window. The identical building is used for the header above the door.
That header is held into place by two jack studs that type the perimeters of the window opening. Beneath these jack studs is the tough window sill that types the underside of the window opening. And that tough window will is held in place by two extra jack studs beneath it, with cripple studs in between to maintain the 16-inch spacing constant.
As soon as the wall wall was framed, they added the all-in-one product that I discussed earlier, which is mainly an insulation/home wrap, OSB, and siding, multi function. They hooked up these in order that the sides of this siding product lined up with the sides of the vertical studs on the ends of this wall.


These items had been nailed onto every stud.


You may see proper right here that these items prolonged previous the underside of the bottom plate by about 5 inches. You too can see what I imply about these items coming proper to the aspect edges of the wall studs on the ends.


Whereas one man completed attaching the all-in-one siding items, one other one used a router to chop out the home windows and the door.


Subsequent, they hooked up this fascia board (strips of the identical all-in-one product) to the entrance fringe of the two″ x 8″ board on the high of the wall. This strip overlapped the highest of fringe of that 2″ x 8″ board by about 4 inches. I didn’t perceive this at this level, but it surely all made sense later.


Right here’s one other view of it trying down on the high of the wall. You may see that he left it prolonged out about 10 inches, and it sticks up about three or 4 inches. This can make sense later. In addition they measured and marked the spacing for the trusses alongside the highest plate of the wall.


Earlier than elevating the wall, they did all the caulking, and in addition put in the home windows. They used flanged new construct home windows that I offered. Earlier than putting in the window, they put a bead of caulk across the high, the perimeters, and about two inches in on both sides of the underside. Then they positioned the window within the opening and hooked up it. The caulk was between the flange and the siding.


They moved so quick that I missed getting an image of them including the trim across the window, however these trim items went proper over the flange of the window and had been nailed in place.
They did each little bit of caulking (each nail gap, each seam, all the things) earlier than elevating the wall. By the point the wall was raised, all it wanted was paint.


And at last, it was time to boost the wall. Earlier than they raised the wall, they hooked up two scrap items of lumber to the bottom body to behave as a cease to maintain them from pushing the wall over the sting of the muse as they raised the wall.


And there it’s. The primary wall (the entrance wall of the workshop) raised into place. At this level, they didn’t nail the wall into place. They simply used bracing to maintain it upright. They didn’t nail any partitions to the subfloor/basis till all the partitions had been in place.


I took this image of the sting view of the wall so that might see why they prolonged that OSB/siding piece previous the bottom plate by just a few inches. It’s in order that it overlaps that backside body of the muse to maintain water out when it rains.


With that entrance wall up, they began on the tip wall. The top proven within the image beneath was fairly easy because it didn’t have any home windows or a door. It’s only a strong wall. However this wall does embody a truss for the roof, so it was a bit totally different from the entrance wall.


Within the image beneath, I’m trying on the wall from the highest down. So the underside (base plate) of the wall is on the far aspect from me. And identical to the entrance wall, it consists of a base plate and studs spaced at 16 inches on heart. However the high (within the foreground nearer to me) is a bit totally different. The highest place consists of two 2″ x 4″ items of lumber, after which they nailed on a 2″ x 4″ piece hooked up vertically. And you’ll see that it extends on every finish about 4 inches. I had no concept what this was for, but it surely was about to make sense.
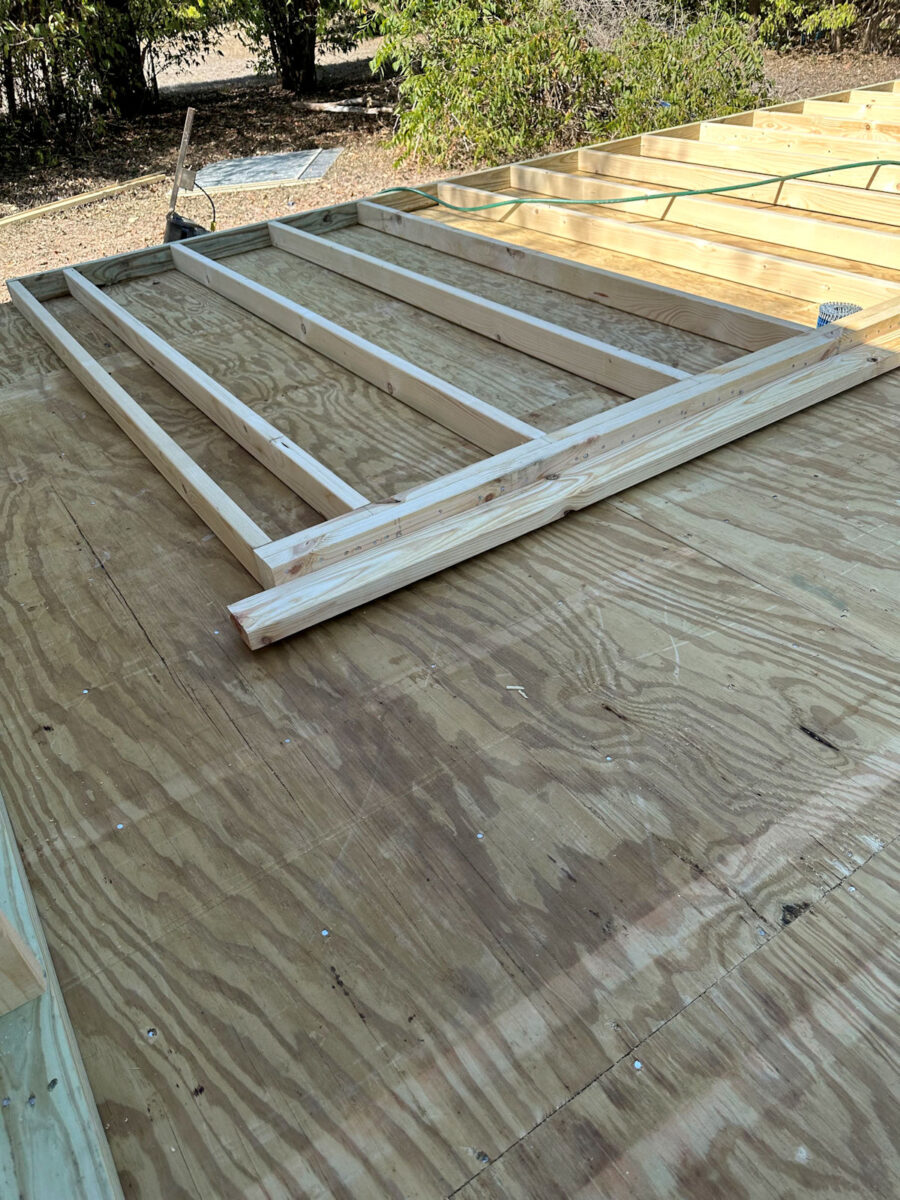
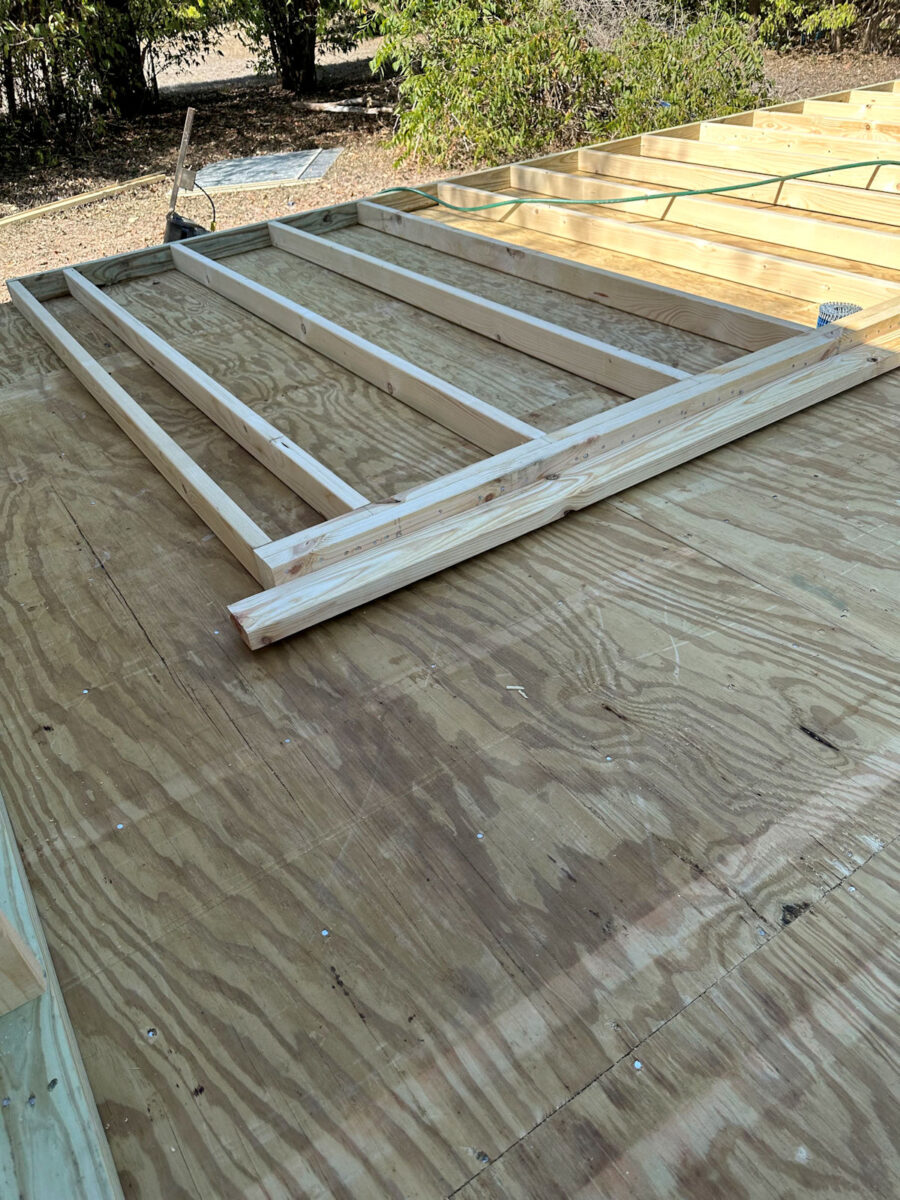
Right here’s a take a look at this wall from the opposite path. You may see that the majority of it’s only a plain, easy wall construction.


So what was that high 2″ x 4″ that was hooked up standing up on its finish used for? That’s what they nailed the tip truss to!


So let me speak in regards to the trusses for a second. This was the one a part of the constructing that arrived pre-assembled. That they had an entire stack of trusses that consisted of three boards — the 2 boards that type the height of the roof, and the cross board that holds them collectively. However two of the trusses (one proven beneath) didn’t have that cross brace holding the angled boards collectively. And people two had been the tip trusses that received hooked up on to the tip partitions.


As an alternative of getting that cross brace holding the aspect items collectively, they hooked up vertical items inside these trusses. The vertical items had been nailed to that very same high 2″ x 4″ piece to which the truss was nailed, after which these items had been nailed into the truss on the high. The highest nails needed to be toenailed in (shot at a diagonal via the brace and into the truss).


I didn’t get an image of the total building of the truss earlier than they raised the wall, however you’ll be able to see a great view of it a few footage down.
And identical to the entrance wall, they did all the building and caulking earlier than elevating the wall. One crucial distinction is that once they hooked up the OSB/siding materials to the aspect partitions, the prolonged the fabric previous the studs on the sting by sufficient to cowl the uncovered studs and edges of the OSB/siding materials on the entrance wall and again wall, so that will be about 4.25 or 4.5 inches. Whereas one completed the far aspect wall, the opposite began on the aspect wall nearer to me.


One factor I didn’t get an image of, however I hope I can clarify right here utilizing this image that jumps forward many steps (attempt to ignore that complicated truth) is that earlier than they raised the aspect partitions, they hooked up a strip of the roof materials (plain OSB) to the highest fringe of the truss, attaching it in order that it was nailed down the middle of the sting of the board, and in order that it stick out a number of inches. You may see that OSB strip right here…


After which to the sting of that strips that caught out just a few inches, they nailed these fascia boards. And once more, this wall all completed earlier than the partitions had been raised, and all the things was caulked and just about completed, aside from paint, when the partitions had been raised.


I additionally wish to level out that this wall with the massive storage door opening was completed precisely like the opposite partitions in that it had a base plate that went the total size of the wall. That base plate was there till all 4 partitions had been raised and put into place. Solely then did they arrive again and use a reciprocating noticed to chop out that base plate. However that plate wanted to be there so as to add stability whereas they raised and moved the wall into place.


Right here’s a view with each finish partitions up. Now you can get a great view of these vertical items they hooked up contained in the truss. They raised these partitions, scooted them over in order that they snugged up in opposition to the entrance wall, after which nailed the partitions collectively from the skin of the constructing, nailing the tip studs collectively all up and down the nook.


As soon as the partitions had been nailed collectively, they added these vertical trim items on the corners.


In addition they added these further non permanent braces holding the entrance wall to the aspect partitions.


At this level, they used a reciprocating noticed to chop away the surplus fascia board from the entrance wall in order that the 2 boards met on the nook, after which they caulked these boards the place they met.


Right here’s a view from the entrance at this stage with the three partitions.


I didn’t take footage of the again wall as a result of it was constructed and raised precisely just like the entrance wall. As soon as it was raised, they nailed it to the aspect partitions and added the skin vertical nook trim.
Constructing the roof
With the fourth wall raised, and since they’d completed the caulking earlier than elevating the partitions, one man began portray the constructing whereas the opposite two began engaged on the roof. I used to be fascinated to look at them do that. They hung all the trusses the wrong way up from the back and front partitions.


After which one climbed up on high of the entrance wall, and the opposite climbed up on high of the again wall, and one after the other, working from my proper to my left, they raised a truss rightside up, positioned it on the marks they’d pre-marked earlier than elevating the partitions, and nailed the trusses into place. And that is the place you’ll be able to see the genius in pre-attaching that fascia board, and why it extends up just a few inches. It extends up the proper measurement in order that it covers the ends of the trusses plus permits for the thickness of the roof OSB. But it surely’s extremely useful throughout this step simply to stabilize the trusses and make it simpler for them to get them positioned and nailed.


As soon as all the trusses had been nailed into place, the opposite man had completed portray the constructing and began engaged on portray the trim whereas the opposite two beginning attaching the OSB to the trusses. Once more, these items had been all pre-cut of their store earlier than they even received right here, so it went fairly rapidly.


And right here it’s! A whole 18′ x 27′ workshop in-built a day!


The following day, they put in the door, shingled the roof, and strapped the constructing to the anchors. I didn’t get footage of any of that course of as a result of these are quite common issues that the majority DIYers know the best way to do (aside from strapping down a constructing, and I simply didn’t wish to get in his approach, however I’m positive there’s a YouTube video exhibiting that course of.) However by watching this constructing course of from starting to finish, I positively discovered just a few issues that I didn’t beforehand know, even with all of my years of DIYing. I truly really feel like I may construct somewhat shed myself now! (So long as I’ve helpers with muscle and no concern of heights, in fact!)
I’m so excited to lastly have my very own workshop. It nonetheless has a protracted solution to go earlier than it’s truly usable, effectively organized, and cute on the skin. However it is a nice begin!


So how a lot did this price? The full for this constructing got here to $21,472.66. That involves $44.18 per sq. foot, which appears about proper for an unfinished constructing that doesn’t have electrical, plumbing, and has an unfinished inside. It’s as much as me to complete the remainder.
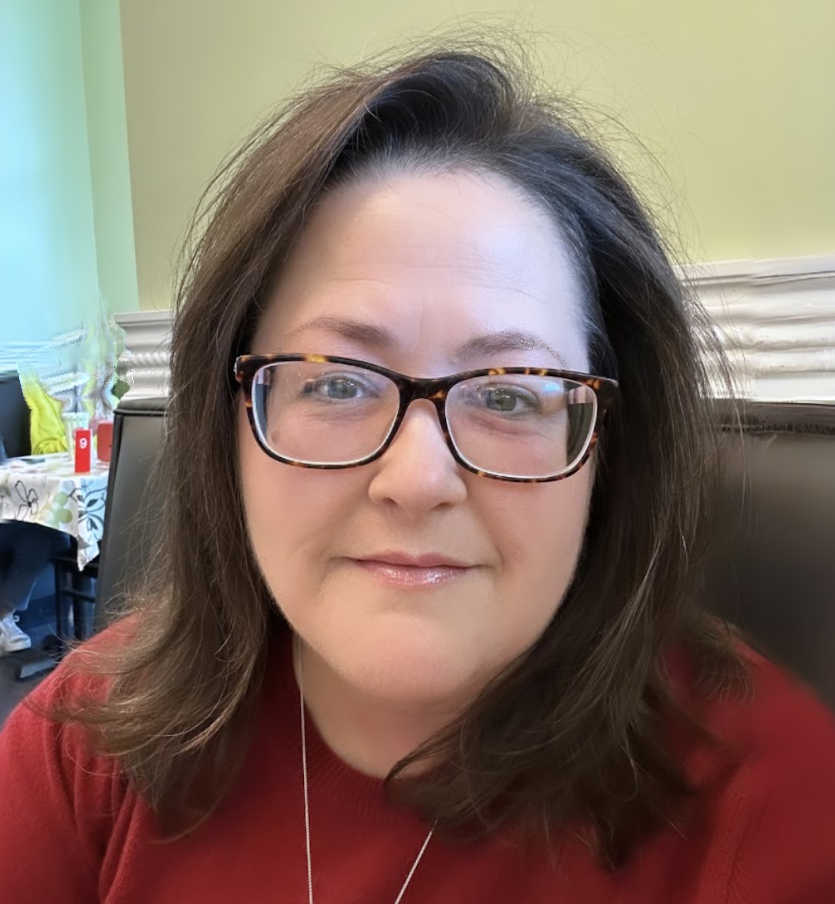
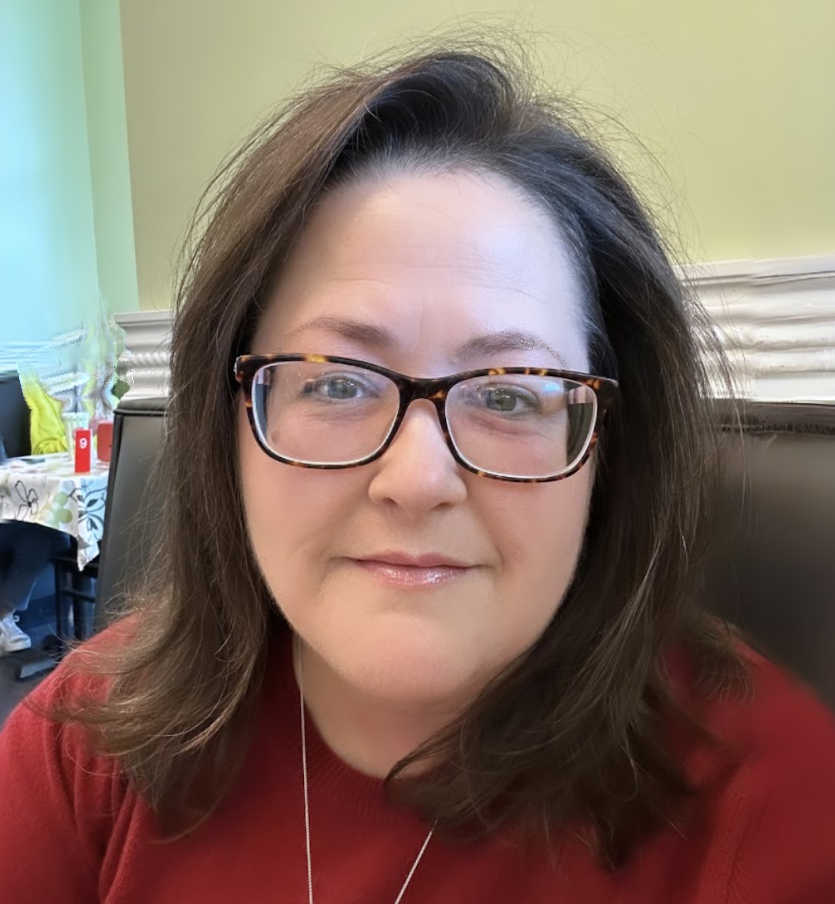
Addicted 2 Adorning is the place I share my DIY and adorning journey as I transform and enhance the 1948 fixer higher that my husband, Matt, and I purchased in 2013. Matt has M.S. and is unable to do bodily work, so I do the vast majority of the work on the home on my own. You may study extra about me right here.