I’m nonetheless specializing in my workshop and making an attempt to get some initiatives executed outdoors earlier than I flip my consideration to our bed room suite. I do know that most likely doesn’t make sense within the minds of many individuals. In any case, we actually don’t have a bed room proper now. We’ve turned our breakfast room into a short lived bed room whereas the rooms that can be our bedrooms suite are underneath building.
So why am I specializing in my workshop? As a result of I wish to. That’s actually it. I’ve fairly the record of initiatives I wish to get executed this 12 months (which you’ll see right here), and I needed to leap in with each toes and get began on my record. And after I obtained began, the initiatives that I felt probably the most motivated and excited to do had been those on my workshop, particularly for the reason that climate was so stunning. And now that the workshop is underway, I’m tremendous motivated to see the outside completed.
We’ll see how far I can get earlier than the climate forces me inside. In any case, that is winter. And regardless that I’m in Texas, our climate can nonetheless get fairly chilly. I’m typically okay with chilly so long as there’s numerous Texas sunshine, but it surely’s a tough “no” for me with regards to chilly and windy, or chilly and moist. So I’m undecided how far I can get, however I’m going to do my greatest to really end it earlier than switching gears. I promise nothing, although. I’ll go the place my motivation takes me.
Anyway, simply as a fast overview, up to now I’ve turned this boring grey constructing…


After measuring the width of the area that I left open within the skirting to get the width of the steps (75″), after which measuring from the bottom to the underside of the metallic threshold on the workshop door to find out the general top of the steps (15″), I sat down at my desk to give you my particular plan, actual measurements, and provide record. I do know that’s gained’t make any sense to y’all, however right here’s a glimpse of how I plan initiatives like this, and the way I determine my provide record.


My plan was to construct these steps immediately on the bottom. That implies that I wanted to make use of stress handled wooden particularly marked for floor contact use. Bear in mind that not all stress handled wooden is created equal. Additionally remember that the workers at Lowe’s are most likely going to be clueless about this. Those on the Waco retailer certain had been. I saved asking the place I might discover stress handled 2×6’s for floor contact, and all of them (three totally different staff) pointed me to the common stress handled lumber that’s particularly marked on the tip with “not meant for floor contact.” This lumber is stress handled, and but, it shouldn’t be used any nearer than six inches from the bottom.


Should you’re going to place lumber immediately on the bottom, you wish to search for stress handled lumber particularly marked for floor contact use.


They really didn’t have any floor contact 2×6’s, so I needed to go for 2×12’s as a substitute. That was positive as a result of I used to be going to have to tear the two×6’s to the suitable width anyway, and I can simply as simply rip 2×12’s. And since I used to be utilizing 2×12’s, I solely wanted half the quantity, so I believe I ended up saving a number of {dollars} ultimately. I additionally purchased PVC boards to clad the stress handled steps, cedar deck boards, 3.5-inch exterior screws particularly labeled to be used in stress handled lumber, a brand new round noticed blade, 5-inch HeadLOK screws to screw the steps to the constructing, deck screws, and mending plates.


The plan was to construct three frames, one for every of the three steps, and stack them. The underside body would have outdoors dimensions of 75″ vast (the width of the area within the skirting) by 54″ deep. However as a result of the lengthy back and front boards had been connected inside the 54-inch-long facet boards, I lower them three inches shorter. That method, as soon as they had been all screwed collectively, the width of the board (72″) plus the thickness of the 54″ boards on either side (1.5″ every) would whole the 75-inch width I wanted to suit contained in the opening within the skirting. After which I lower the interior helps to 51″.


That 54-inch measurement will permit for a 30-inch-deep prime step/stoop, and 12 inches for the center and backside step, for a complete of three steps, every 5 inches excessive, to succeed in the 15 inches whole top that I had from the bottom to the metallic threshold of the door.
To tear the two×12’s to the suitable top, I used my round noticed with a rip fence connected. That is the precise round noticed I’ve (affiliate hyperlink), and it did a superb job and made very simple work of ripping this 2×12 lumber. And please take pleasure in this nonetheless shot from my video. I selected it particularly as a result of it made me snort so exhausting that I caught Tiger mid-jump.


I additionally wish to level out that since I needed every step to be 5 inches, I ripped the boards for the underside body to 4″. Since this backside body could be sitting immediately on the bottom, that 4″ top plus the 1″ deck board would give me a top of 5 inches for step one. However on the following two frames, I ripped the boards to five″ as a result of 1″ of that body could be misplaced behind the 1″ deck boards on the earlier step. Right here’s a side-view illustration to point out you what I imply.


With my boards ripped to the proper top and size with the round noticed, I put them collectively utilizing the three.5″ exterior screws labeled to be used with stress handled wooden.


After which I added three inner helps for every body. I needed these spaced not more than 16″ aside, which is the spacing used for flooring joists on a home. Mine ended up being spaced 15″ aside.


And I screwed these to the body utilizing two screws on either side.


Right here’s what that first body seemed like in place sitting contained in the opening of the skirting.


I constructed the second body in the very same method, however this one was 42″ deep to permit for a 12″ depth for step one.


After which the third one was the identical course of, however 30″ deep to permit a 12″ depth on the center step and a 30″ depth on the highest step/stoop.


After I tried to stack them the primary time, I spotted that I had gotten forward of myself. Earlier than the three bins might be stacked and secured to one another and to the constructing, I wanted to chop away and take away the entire trim boards that had been beneath the metallic threshold. I used a scrap piece of lumber as a straight edge, lined up underneath the edge, to attract a line the place I wanted to chop the facet door casing boards, after which used my Dremel Multimax (affiliate hyperlink) to chop and take away the boards.


With these trim items gone, that allowed the bins to stack correctly proper towards the constructing.


And you’ll see right here the way it sat flush towards the siding with the trim items eliminated.


Then I had one other downside, but it surely was one which I had been anticipating. The bottom wasn’t completely stage (stunning! ), and I wanted to make use of my shovel to do some leveling in order that the deck board would sit slightly below the metallic threshold. You may see beneath that with out leveling out the bottom, the deck board didn’t match correctly underneath the edge.


And the entire construction was barely unlevel — larger on the left facet and decrease on the suitable facet.


Right here’s a greater view of what I used to be beginning with.


Earlier than I moved issues round and began digging within the grime, I made a decision to go forward and fasten the frames to one another. I used these mending plates to do this.


These plates are extremely sharp, and they’re typically used for holding lumber collectively to type trusses and issues like that. They’re typically connected utilizing a hydraulic press, however you can even connect them utilizing a hammer. It gained’t be as fairly and ideal as these connected with a hydraulic press, but it surely’ll do the job. I used my 3-pound hammer to connect these, and it made the job fast and simple. I used a complete of 14 mending plates to carry the frames collectively.


With the entire construction put collectively, I used to be then capable of dig out the grime till I had the left facet low sufficient to suit a deck board between it and the edge.


And I additionally had the entire thing fairly near stage.


After I put the deck board on to check for match, the suitable facet was about 1/4″ too low, so I used 8″ composite shims (as a substitute of wooden shims, which might rot towards the bottom) to shim up the suitable facet till it was stage. These elements of the shims which can be protruding could be lower away, or they will simply be hidden with mulch.


As soon as the suitable facet was shimmed, it was as near completely stage as I used to be going to get it.


As soon as the construction was in place and stage, I used these 5-inch LedgerLOK screws to safe the steps to the constructing.


Right here’s a detailed up have a look at the LedgerLOK screw. This stuff are huge and powerful. There’s no method my steps can be transferring with these holding them in place.


I used 4 whole, one in every part of the body, to safe the steps to the constructing.


After which I used to be lastly prepared to connect the deck boards. I lower the deck boards to the width of the body plus 5 inches for a 2.5″ overhang on either side. As soon as the gorgeous PVC boards are connected, that may give me a completed overhang of 1.5″ on either side. I began with the entrance board (i.e., the board furthest away from the constructing) and I connected it with a 1.75″ overhang on the entrance of the step. Once more, as soon as the PVC boards are connected, that may give me a closing overhang on the entrance of three/4″. After which I labored my method again in direction of the constructing.


Right here’s a have a look at the progress with the primary 4 boards connected. (Sorry for my finger! I don’t know what occurred there. )


The ultimate board needed to be ripped to a narrower width to suit. I used my round noticed with the rip fence to chop that board, after which slid it in underneath the metallic threshold.


And right here’s the highest step executed!


I repeated that on the opposite two steps, once more beginning with the boards closest to the entrance of the steps (i.e., furthest away from the constructing) and labored my method again. These steps additionally required the ultimate boards to be ripped to a narrower width.


And right here’s the essential construction completed!




I’ve no plans so as to add handrails to those steps. They’re very brief steps and solely whole 15″ in top, so at the least for now, I see no want in having a hand rail. If somebody with mobility points needs to enter my workshop, they will achieve this very simply utilizing the facet ramp.


That’s the place I had deliberate to cease for the day, however I made a decision to go forward and get one coat of stain on the steps earlier than calling it quits for the night. That method, the stain would have loads of time to dry earlier than I added the gorgeous PVC boards. I actually didn’t wish to get stain on these PVC boards. I used to be just about working at nighttime to get that coat of stain on, so I needed to do some picture enhancing magic to brighten up this image sufficient to point out the steps as soon as I completed the staining course of. The colours positively aren’t correct. I used Cabot Australian Timber Oil, and I can’t keep in mind the colour. This isn’t the ultimate shade I would like, so the steps will want a second coat of a unique shade.


So all that’s left after that is to clad the frames with the PVC boards to make them appear like our entrance steps. Keep tuned for the ultimate workshop steps!
If you wish to sustain with my 2025 record of house targets (and my progress with hyperlinks to completed initiatives!) you may see that right here: 2025 Grasp Checklist of Dwelling Objectives
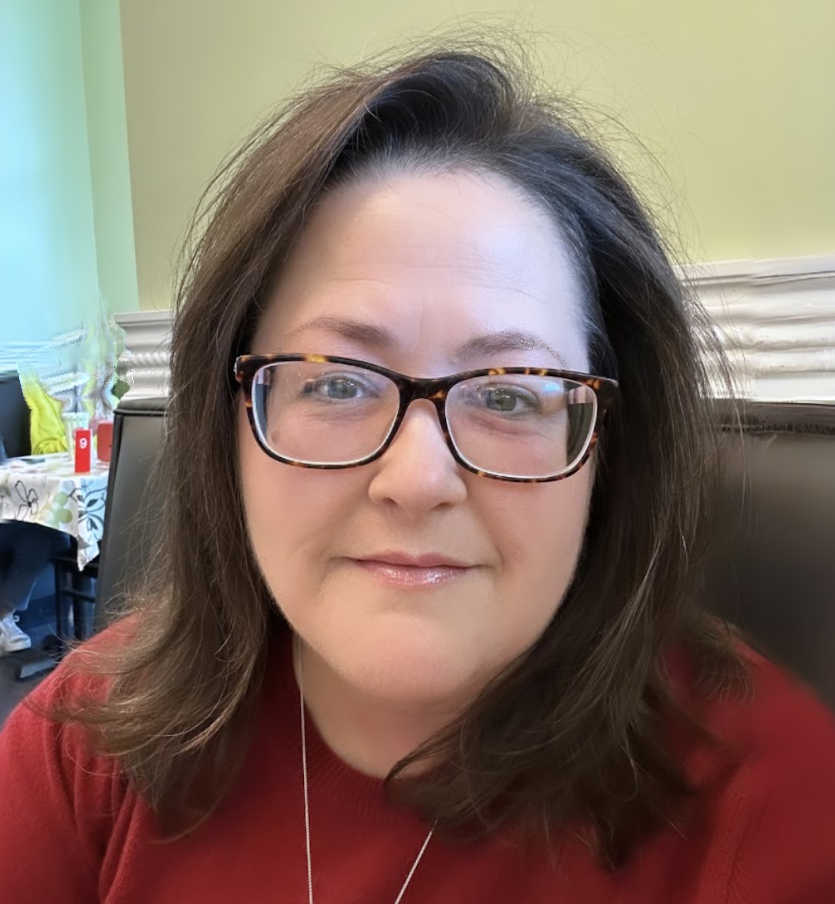
Addicted 2 Adorning is the place I share my DIY and adorning journey as I transform and embellish the 1948 fixer higher that my husband, Matt, and I purchased in 2013. Matt has M.S. and is unable to do bodily work, so I do the vast majority of the work on the home on my own. You may be taught extra about me right here.